Driver Support Is Key to Electric Powertrain Adoption
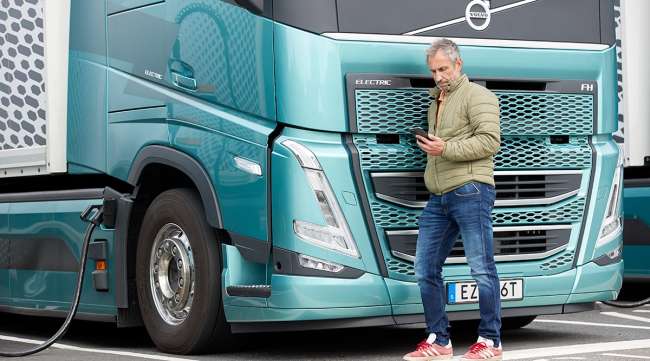
[Find the latest in equipment & maintenance: Explore this quarter's issue of Calibrate]
As a diesel lover, I expected my experience driving a Class 8 truck with an electric powertrain to rank between boredom and dreadful. But a trip to Gothenburg, Sweden, revolutionized my thinking.
At the worldwide headquarters of Volvo Trucks, I had my first opportunity to drive an electric truck. The tractor was a European Forward Control-High Entry (FH) cabover piloted around the facility’s customer test track. The vehicle was equipped with a 660 horsepower, three-motor powertrain that drove through a standard Volvo 12-speed transmission. As I turned onto the track and applied throttle (or amperage!), the truck climbed almost silently, steadily and rapidly up to highway speeds, using just gears 7, 10 and 12, providing an extreme level of torque. It was exhibiting a gracefulness and speed of acceleration I’d never before dreamed of in a Class 8 truck.
I also took the Class 8 FH tractor around a different circuit, stopped on a steep hill and tried a heavily loaded uphill start. The smoothness and power during the start, and the tractor’s ability to slip gracefully from gear to gear even climbing a steep hill, sold me on electric powertrains.
After that experience, I believe that one of a fleet’s greatest incentives for going to battery-electric technology has to be driver retention. Considering the performance, quietness and overall feel of these vehicles, driver satisfaction was at the core of every design decision providing a win-win for them and the fleets.
More Q1 Calibrate
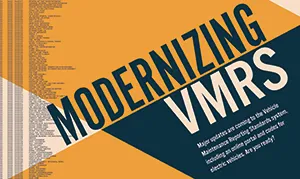
►VMRS Portal Is Nearly Here
►Freeze: Our Electric Future: You Don't Have to See It to Believe It
►Five Questions: Craig Provonsha
►Industry Needs Agreement on Future of Trailer Connections
►Baxter: Driver Support Is Key to Electric Powertrain Adoption
Explore the Issue!
According to “The American Diesel Locomotive” by Brian Solomon, modern electronics first revolutionized diesel-electric locomotives because alternating current, properly processed to vary its frequency, can drive motors with unprecedented smoothness and efficiency throughout a wide range of rpms, unlike earlier direct current motors. The smoother torque the new AC motors produced allowed railroads to use fewer locomotives to haul a given load while saving a lot of fuel.
This same technology enables electric truck powertrains to haul freight using minimal electrical energy, provide a level of torque drivers haven’t experienced, and, as you have undoubtedly heard, reverse the motors and recharge the batteries rather than wasting inertia during stops. Also, since motors can be almost instantly brought to a precisely controlled rpm, upshifts can occur during acceleration much more quickly than with diesels. Thus shifts are rapid and seamless. Mack Trucks even has a “two-speed, powershift transmission,” according to Scott Barraclough, senior product manager for e-mobility, which makes electric shifts even more seamless.
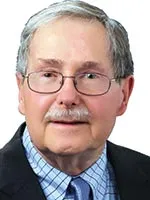
Baxter
Diesel technology evolved from balky machines needing to run within a narrow rpm range, requiring hundreds of shifts in a trip to far more flexible power plants providing enough torque rise to minimize driver effort even before automated gearboxes were introduced. The electric transition will bring a second and similar revolution to truck powertrains as electric motors with similar horsepower ratings provide far more torque, and can put it to the wheels even from zero rpms.
Look Ma, No Clutch!
Torque rise, of course, refers to an increase in torque that compensates for a drop in rpm. The result was that high rpm was no longer needed to create diesel horsepower and acceleration — hence downspeeding. A typical premium diesel specification today might be rated at 500 hp and 1,850 pound-feet of torque. But, for example, Mack’s Barraclough says a dual-motor Mack LR Electric powertrain provides 448 peak hp and 4,051 pound-feet of torque. Volvo’s two-motor electric powertrain produces similar numbers — 455 hp and 4,051 pound-feet, but a torque and horsepower chart shows continuous full torque from 0-4,000 rpm, and then an absolutely flat horsepower curve delivering that 455 rating from 4,000 rpm up to more than 10,000. Detroit’s powertrain shows a similar curve with peak torque lasting till the motor rpm passes 4,000 and horsepower remaining constant through 10,000 rpm.
Compact and powerful electric motors retain efficiency at much higher rpms than a diesel, which means axle ratios that multiply that torque a great deal more than in diesel drivetrains, too.
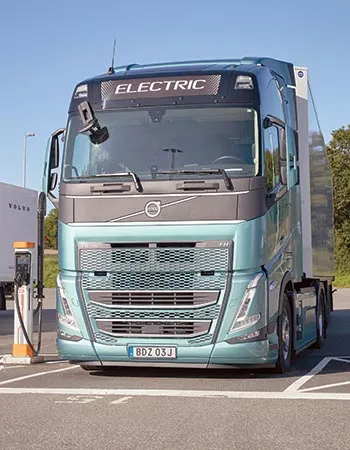
Volvo's FH Electric (Volvo)
The heavier-duty electric powertrains universally provide two basic transmission ratios. An upshift occurs in the mid-20s, though the exact shift point will vary with load and grade. But there are subtleties in the layouts that bode well for extreme performance even though diesels run best with at least 10-12 forward speeds. Two speeds doesn’t sound like enough. However, Volvo has a very unusual transmission that plays gearing tricks to optimize torque and horsepower inputs, although its shift collars and pneumatic actuators are conventional. John Moore, product manager for electric vehicles, described a gearbox that provides two split main drive ratios. In first gear, one motor drives through a countershaft, while the other drives through the main shaft. The faster motor has a ratio of 9.26:1 while the slower motor drives at a 3.67:1 ratio. In second, both motors drive the mainshaft, but the power is still split, allowing one motor to turn about 1,000 rpm faster than the other with the transmission ratio for the slower motor being 3.52:1. Axle ratios are 3.91:1 for straight trucks and 4.56:1 for tractors.
Another illustration of the use of gearing is the overall ratios provided by the Detroit system, which were provided by Kevin Otzenberger, e-mobility product marketing senior analyst. The two overall ratios for tractors work out to 46:1 in first and 16:1 in second.
The smoothness and power during the start, and the tractor’s ability to slip gracefully from gear to gear even climbing a steep hill, sold me on electric powertrains.
John Baxter
The mainstream manufacturers provide various arrangements of the drive components, though much of the mechanicals are familiar. Volvo’s system has its two motors and transmission combined in a unit that mounts between the rails under the cab, with a standard tandem axle drive using the normal two driveshafts. Mack has two electric powertrains. The LR has two motors in a single unit that incorporates a “purpose-built EV transmission and not a normal diesel gearbox,” giving that ability to shift under power. A standard tandem axle drive arrangement follows, but Mack’s Medium-Duty Electric, used often by trash haulers, with 260 hp and 1,850 pound-feet of torque has a direct drive from a single motor to the single rear axle.
Detroit Diesel’s Otzenberger says e-axles that combine motor, transmission and a modified standard axle and differential gearing in a single unit are used, with wiring carrying the energy to them rather than driveshafts, hence the numerically higher overall ratios mentioned above. The Detroit system provides either single- or dual-motor axles, with 195 and 395 hp, respectively. A tandem axle tractor will incorporate one dual-motor axle with a single-motor axle to make 590 hp total. Otzenberger noted that torque output figures at the wheels for the single and dual motor arrangements at 11,500 and 23,000 pound-feet.
One other large advantage of electrics is freedom from noise and vibration. Otzenberger mentioned drivers telling him they mostly hear the tires at highway speeds, or a pair of pliers rattling in the glovebox, and one said he might delay retirement driving electric trucks. Volvo’s Moore mentioned drivers have an easier time talking to their dispatchers and hearing sirens or car horns nearby. Mack’s Barraclough said simply, “I can confidently say that electric vehicles are noticeably quieter in the cab than their diesel counterparts, and that is one of the first eye-opening comments I get from operators.”
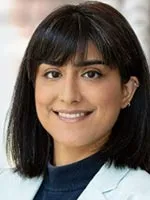
Chadha
Parul Chadha, global product management and strategy leader of ePowertrain at Accelera, noted that electric vehicles have huge advantages in terms of noise, vibration and harmonics, which a driver can sense immediately while idling and driving at low speeds while in the inner city.
“On a highway drive, the most noise in a driver’s cab will come from the rolling resistance of the tires as well as from good or bad aerodynamics rather than the electric motor,” she added.
Scott Newhouse, chief engineer with Peterbilt Motors Co., provided an actual decibel measurement of in-cab noise level at full acceleration at 55 mph in a Peterbilt 579. With an X15 engine the noise level was 78 dBa while in a 579 battery-electric vehicle with the Meritor e-axle, the measurement was 70 dBa — a noticeable difference.
Electric powertrains offer rapid acceleration, a far more benign in-cab environment, regenerative braking that often actuates as the driver releases the throttle without service brake actuation and is adjustable, and even the ability to just plug the truck in rather than standing there while the tanks are filled during refueling. Thus, it seems electric trucks are very likely to not only improve a fleet’s carbon footprint, but to greatly ease the perennial problems many fleets have with driver turnover.
Want more news? Listen to today's daily briefing below or go here for more info: