Fleets Implement Techniques to Fight Corrosion From Salts
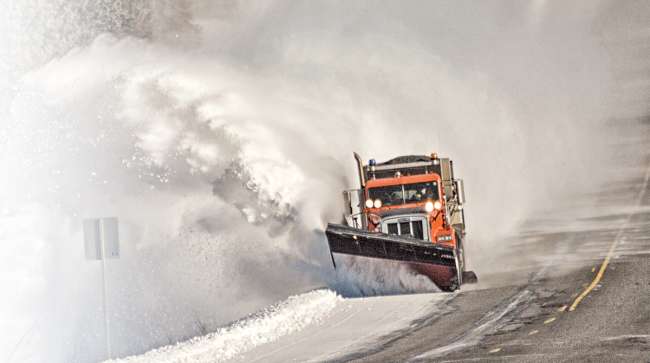
[Stay on top of transportation news: Get TTNews in your inbox.]
Keeping roadways free of snow and ice is critical for safety, but the de-icing products states use — mainly chlorides — are notorious for causing truck corrosion, creating a significant risk to equipment. Meanwhile, fleets are working to fight corrosion by spec’ing certain materials, inspecting equipment regularly and washing it frequently.
Kirk Altrichter, executive vice president of fleet services for Kenan Advantage Group, said the de-icing chemicals are a constant maintenance concern. “Between sand, calcium chloride, magnesium chloride and road salt, you could develop quite a paste, which is hard to remove and helps to keep the moisture in and cause corrosion more rapidly,” he said.
Trying to reduce corrosion is becoming increasingly important as OEMs turn to new and different materials that can react differently to chlorides, said Jack Legler, technical director of American Trucking Associations’ Technology & Maintenance Council. “The ice melting formulations might not change significantly, but the stuff on the truck is changing. You need to be aware of the impact of what is going on there,” he said.
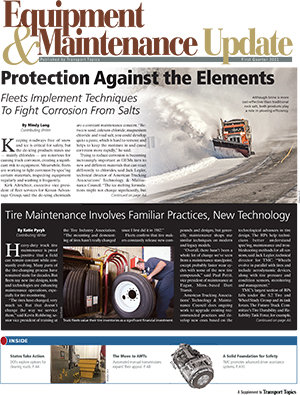
- Fleets implement techniques to fight corrosion from salts
- State DOTs find alternative solutions to clearing roads
- Tire maintenance involves familiar practices, new technology
- Automated manual transmissions become industry's popular option
- Braswell: Keeping a solid ADAS foundation
- Freeze: Trucking is the line between other industries
Chris Sterwerf, chief operating officer of Fairfield Auto & Truck Service Inc., a maintenance and repair shop based in Fairfield, Ohio, said that as vehicles become lighter to achieve fuel-efficiency goals, manufacturers are using materials in different ways.
That is raising the stakes for preventing corrosion.
Engineers use stronger steels in frame rails with a much higher tensile strength that allows for a single rail per side instead of two or three rails per side, Sterwerf said. “One risk with this is that corrosion protection must be taken more seriously because the corrosion doesn’t need to eat through as much material as the two or three rails per side,” he said. “The metallurgy of the rails can change as tensile strength becomes higher, and some corrosion-resistant properties can be lessened.”
Cabs are being light-weighted, which creates additional risk, Sterwerf said. “Each spot weld holding the cab together is designed to protect the occupant and limit the degradation of the survival space in the event of a rollover or crash,” he said. “As the metal panels change in shape and structure to reduce weight, more emphasis and responsibility is being placed on the joining methods.”
Welding, grinding, heating and drilling on these trucks create hot spots that open the door for corrosion to creep in and severely weaken the welds and structure that hold together the occupant’s survival space, Sterwerf said.
The danger zone for corrosion on a truck and trailer is about 4 feet up from the ground. “That is the hot zone from corrosion activity,” said Brian Herrington, area sales manager for Atro Engineering Systems. “Anything metal is going to rust, and anything rubber is going to look like it is dry rotting.”
Thomas Peters, maintenance research and training engineer for the Minnesota Department of Transportation, said the areas most susceptible to corrosion include structural parts, components and equipment in places where dirt and other material deposit and remain wet. Those include metal folds and joints, breaks in painted surfaces, threaded screws and beneath coatings that do not adhere well to the surface.
“These underbody components commonly experience pitting, crevice, galvanic and cosmetic corrosion,” he said.
What’s more, the use of dissimilar metals causes galvanic corrosion, noted Laura Fay, research scientist and program manager for cold climate operations and systems and infrastructure longevity and sustainability at Montana State University’s Western Transportation Institute.
“Instead of the salt just eating away at it, you get these electrical cells forming due to contact between the different types of metal, so you get more corrosion, and it is harder to fix,” Fay said. “If you can prevent the salt from reaching the metal, it is going to last longer.”
Sterwerf said aluminum panels with steel fasteners, with no or very little barrier between the two, create an expensive problem over time. “When a vehicle is being repaired, and the manufacturer uses dissimilar metal fasteners, it’s usually a good idea to apply a product with a zinc-rich suspension on the fastener before replacing it in the hole,” he said, explaining that the zinc will act as a sacrificial lamb and corrode, creating a protective coating that isolates the steel from the aluminum.
Kenny Junkin, chairman of TMC’s committee on corrosion, said one of the largest concerns is corrosion that occurs on and underneath hidden items. In addition, de-icing chemicals can make their way into the cab through a bad seal or on a driver’s feet. “They can eat up the metal, like the screws that hold your thresholds down. Eventually, if it is an old enough vehicle, it can eat out the floorboards,” he said.
Junkin added that if there is a bad seal, de-icing chemicals can get through the wiring and corrode it. “That is in addition to the damage it is doing to the metals inside your cab.” He explained that corrosion within wires could be hard to find and replace because wiring harnesses are grouped tightly.
Scott Allen, director of fleet assets and maintenance for Dupré Logistics, said the fleet adds extra wraps to some of its wire harnesses for additional protection. “Along the inside of the frame rail, we spec brackets that push the wire harnesses out from touching the inner part of the bracket,” he said. “When it is laying inside of the frame rail, it is an avenue to build up grease, dirt or other materials that can create problems.”
Fleet Solutions
In certain applications, Dupré Logistics, which is based in Lafayette, La., and ranks No. 90 on the Transport Topics Top 100 list of the largest for-hire carriers in North America, sprays all the rails and undercarriage in military-grade paint.
“We put that on bumpers, spray under the cab and on the frame rails. That helps fight the corrosion,” Allen said. “Any moisture can be a killer.”
To help reduce corrosion, Junkin said the fleet he works for buys trucks that are blasted, primed and then painted.
Herrington said spec’ing the right materials when purchasing equipment can help cut costs later. “You’re going to pay the piper at the back end or the front end. It is a lot more expensive to pay the piper at the back end,” he said.
Some materials are becoming more cost-effective for fleets. For example, polyurethane can be used almost anywhere there is a rubber item, such as engine mounts, radiator mounts, hood latches, hood rollers and fifth wheels. “Years ago, polyurethane was too expensive to consider, but now the price has come so far down the price is basically the same,” he said.
Kenan Advantage Group, which is based in North Canton, Ohio, and ranks No. 22 on the for-hire TT100, specs equipment with stainless, galvanized or aluminum components to avoid the damage more common with carbon steel. If the equipment is repaired and did not come with stainless, galvanized or aluminum parts, the fleet tries to replace items with those materials, Altrichter said.
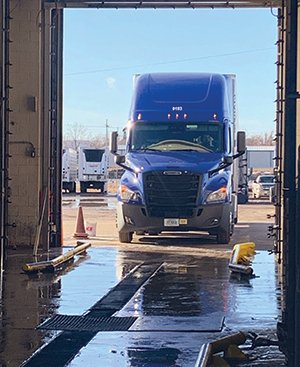
Fleets such as Grand Island Express have added an on-site wash bay that uses auto-grade detergent and water to help fight corrosion. (Grand Island Express)
Deen Albert, director of operations for Grand Island Express, said the suspension, the running gears and the framework on the trailer can rot away quickly as well. Grand Island Express specs trailers with self-healing coating on the suspension.
Some of the biggest challenges are the smaller areas with connections and bolts. “There isn’t much you can do to spec that away. It is an area we pay a lot of attention to when we clean tanks and do preventive maintenance,” Dupré Logistics’ Allen said. “Anywhere stuff can sit, whether it is moisture, dirt, grease or a chemical, is what we try to watch for.”
MnDOT uses several preventive maintenance techniques, including washing, inspecting equipment for rust spots and treating them appropriately, greasing contact points, storing equipment in dry environments, not overloading equipment with solid or liquid de-icers, using salt removers or salt neutralizers after storms, and establishing supervisor spot checks to ensure that preventive maintenance procedures are being followed, Peters said.
One of the best tools to minimize corrosion is regular washing, Ohio Department of Transportation spokesman Matt Bruning said. ODOT washes its trucks with soap and water frequently to keep corrosion at bay and recommends that everyone do the same in the winter. “We’ve tested a variety of anti-corrosion products, and honestly, soap and water is just as effective as anything,” he said.
Grand Island Express, based in Grand Island, Neb., added an on-site wash bay that uses auto-grade detergent and water to help fight corrosion, and tractors and trailers go through that wash bay weekly. “That has extended the life cycle of our trailers by about three years,” Albert said.
Dupré Logistics also has on-site pressure washers at some of its locations to clean equipment. “I’m a strong proponent of regular washing, even if it is just spraying it off,” Allen said.
TMC’s Legler said it ultimately comes down to making sure everything is clean. “Make sure you maintain all of your coatings and maintain connectors,” he said.
Despite the corrosive properties of chlorides, Dan Schacher, Fairbanks maintenance district superintendent for the Alaska Department of Transportation and Public Facilities, said his goal is to keep people moving.
“The trucking industry and the public are our customers,” he said, “so we’re trying to do the best we can to serve them.”
Want more news? Listen to today's daily briefing:
Subscribe: Apple Podcasts | Spotify | Amazon Alexa | Google Assistant | More