Product Manager, Volvo Trucks North America
Perspective: As EVs Evolve, Don’t Overlook Aerodynamics
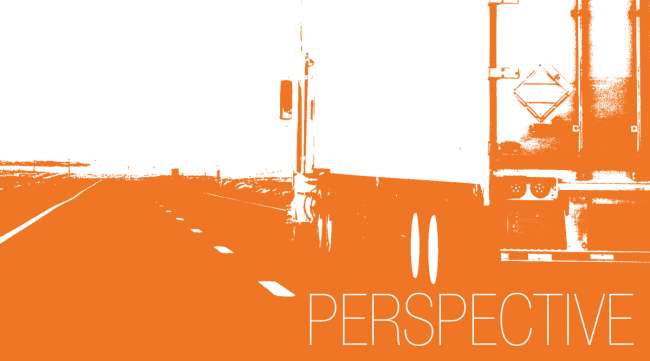
[Stay on top of transportation news: Get TTNews in your inbox.]
The electrification of the trucking industry is attracting a lot of publicity as a way for fleets to decrease fuel costs and improve their environmental performance, but this transition is poised to take many years to fully realize. Right now, fleets looking to improve the efficiency of their operations should not overlook how improving the aerodynamic properties of their trucks can generate immediate returns.
As carriers pursue lower energy consumption across all drivetrain platforms, the rolling population of about 3 million Class 8 diesel trucks in North America offers an immediate opportunity to improve efficiency and decrease emissions.
Aerodynamic upgrades can save fleets thousands of dollars per truck on fuel annually, as air resistance can account for as much as a third of fuel consumption on a typical longhaul operation. Fleets can benefit from improved aerodynamics by using specifically designed components to reduce drag and streamline their trucks.
This is also true for trailers — particularly for dry vans and refrigerated units. Some of these changes are even being mandated, such as the California Air Resources Board’s requirement for standard side skirt fairings under the trailer.
Efforts such as these can advance a carrier’s freight efficiency, which is heavily dependent on streamlining airflow for the truck and trailer.
Regarding airflow, we need to think of the tractor and trailer as a team. The biggest gains will come from sealing the tractor-trailer gap, sealing off the trailer underside and adding a trailer tail. The importance of aerodynamics increases with a truck running at highway speeds, and drivers will find that less throttle is needed to maintain speed after making these improvements to decrease drag, which will lead to fuel savings.
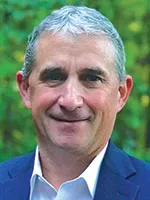
Stadler
To decrease the impact of air resistance, the truck body design must delay or minimize airflow separation, which is when a layer of air detaches from the truck’s surface and becomes highly turbulent, causing a wake and increased drag.
Looking at the tractor, modern aerodynamic designs are available for side mirrors, cab extenders, roof fairings, lower front bumpers, full chassis skirts (which can include drive wheel fairings), wheel hub covers and more.
A top priority should be to make sure the roof fairing is aligned to the height of the trailer, which can require adjustment. The next priority is back-of-cab extenders (also known as trailer gap fairings) to reduce the turbulence between the cab and the trailer. Some of the most effective extenders are designed to deploy on the highway and retract at low speeds to ensure sharp turns don’t cause the fairing to bump the trailer.
Another popular spec option is full side chassis fairings that cover the fuel tanks, which can include small deflectors between and behind the drive wheels to control airflow. One future advance could be a movement toward cameras to replace side mirrors, with in-cab LCD screens to display surroundings, which has the potential to reduce drag.
Next, let’s examine modern trailer modifications, including nose cones, trailer underbody skirts and trailer tails. All these improvements will save fuel.
VTNA President Peter Voorhoeve outlines how the truck maker is helping its customers make better use of telematics and remote diagnostics tools to run their fleets more effectively. Tune in above or by going to RoadSigns.ttnews.com.
One of the main sources of drag is the back of the trailer, where air separating from the trailer creates a low-pressure zone that pulls on the trailer. Fleets can address this and gain about 4% fuel efficiency with a trailer tail, according to EPA SmartWay tests. Tails can extend up to 5 feet behind the truck, angled toward a point to smooth out the wake. Tails that automatically extend as the rear trailer doors are locked are most likely to be used because drivers may forget to take the extra step of extending tails manually.
Plus, not all fleets like tails because they can be damaged if the driver backs into an object with them extended. If that’s a concern, there are alternative devices that are smaller, fixed and mount to the back edges of a trailer to direct air. Another solid choice is upgrading the underbody trailer skirt with a more efficient design.
We recommend carriers take the opportunity to invest in aerodynamic improvements — we predict it will lead to reduced fuel expenses.
Chris Stadler is product manager for Volvo Trucks North America and is integrally involved in aerodynamic optimization of Volvo’s Class 8 trucks. Learn more about Volvo Trucks at volvotrucks.us
Want more news? Listen to today's daily briefing below or go here for more info: