Increased Demand Drives Efficiency in the Cold Chain
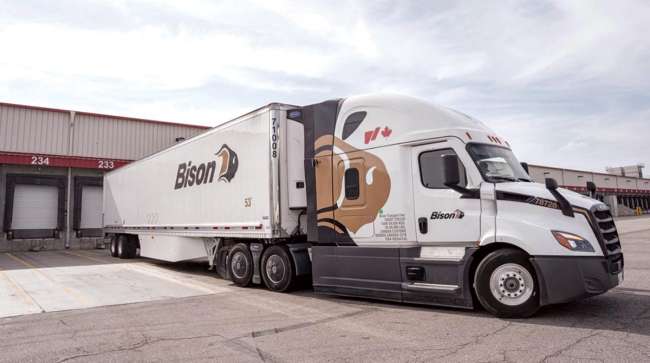
[Stay on top of transportation news: Get TTNews in your inbox.]
As demand for the cold chain continues to increase, so does the desire to control costs, say refrigerated freight experts. The need to increase efficiency and maintain equipment, while also improving sustainability as fleets meet stricter regulatory requirements and customer expectations, has become the priority.
“Our customers are forecasting a higher demand on fresher foods, meaning carriers who want to be competitive must have an efficient cold chain in their fleets,” said Chris Spence, manager of refrigerated operations for Bison Transport.
This scenario can be challenging in refrigerated transportation, said Don Durm, vice president of customer solutions at PLM Trailer Leasing and chairman of the Global Cold Chain Alliance. “The supply chain is very fractured. We have a lot of handoffs, and we’re all trying to meet our deadlines and our budgets,” he added.
Mike Roeth, executive director for the North American Council for Freight Efficiency, said it isn’t just fresh and frozen products driving cold chain growth. Electronics, flowers, pharmaceuticals, and beauty and hygiene items, such as shampoo, also require refrigeration. “It is a larger part of the market than people realize,” he said.
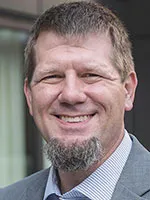
Starks
Tim Schmeits, director of reefer product engineering for Great Dane, said demand for trailers and truck bodies is increasing. “We expect it will continue to increase, and we are gearing up our production capabilities to meet this demand,” he said.
Jonathan Starks, CEO of FTR Transportation, said production of refrigerated trailers in May was roughly 4% higher than in May 2022, on top of the nearly 25% yearly increase from May 2021. “Refrigerated units are getting produced at a strong clip, and the underlying demand for the equipment remains robust. This is despite the weakness that we are seeing in the overall freight markets,” he said.
Yet despite strong levels of current production, backlog levels are on the rise. “Compared to May of 2022, the number of ordered but unbuilt units has actually increased — by only a nominal amount, but it is up,” Starks added.
The backlogs are creating lengthy waits. “We’re out about a year on a single-temp trailer and two years for a multi-temp trailer,” Durm said, adding that cancellations have eased the time on some single-temp trailers to eight months.
One of the challenges is that refrigerated trailers are unique. “Nobody builds a refrigerated trailer. Somebody builds a box. Someone else builds a TRU [transport refrigeration unit]. Somebody else builds a bulkhead inside the trailer, a return head inside the trailer, a ramp, a roll-up door,” Durm explained. “Everything is engineered into the refrigerated trailer itself.”
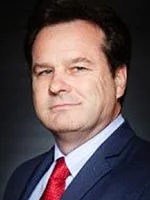
Durm
Since companies are holding assets longer, maintenance has increased, and running older equipment also affects efficiency, Durm noted. Insulation can degrade over time, meaning reefer units must run at high speeds for longer periods to maintain temperature. “If you have an asset you’re holding for extended years, it is paid for, but it is utilizing more fuel,” he said. “A brand-new trailer might get .6 gallons for run-time hour. An older trailer, I can see it going to 2 to 2.5 gallons an hour.”
Reefer Innovation
Great Dane’s vice president of engineering, Chris Lee, said new technology in refrigerated trailer equipment includes thermal efficiency improvements, prevention of insulation degradation, and electronic sensor technology that can gather data and information about the equipment regarding performance and maintenance requirements.
Great Dane’s ThermoGuard technology prevents insulation degradation by preventing out-gassing and moisture intrusion, extending the life of the insulation, Lee said. Great Dane’s studies show that reefers with traditional liners can lose up to 25% of insulating capability — up to 10% within the first year alone — from out-gassing effects.
Bill Maddox, senior manager of product management at Carrier Transicold, truck/trailer/rail Americas, said each new generation brings improved performance. The latest trailers in its X4 and Vector series use an advanced version of the smart engine used in the company’s existing trailer platforms. “The engine’s common-rail fuel injection optimizes fuel delivery, reducing fuel consumption by 5% to 10%,” he said.
Carrier Transicold’s eco speed automatically decreases TRU engine RPMs when possible, improving efficiency compared to normal low-speed operation. The performance enhancements demonstrated 20% to 25% average fuel savings for X4 7700 units, relative to standard X4 units, Maddox said.
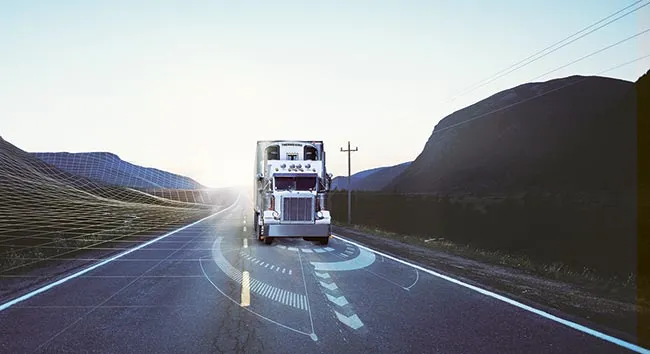
Connected solutions allow refrigerated operations to ensure product integrity through the cold chain and help predict equipment disruptions. (Thermo King)
A major initiative to improve energy efficiency is variable-speed technology in TRUs, such as variable-speed fans and drives. “Improved controls technologies are also helping to get more performance from the unit using less energy,” said Tyler Luzinski, product manager of trailer for Thermo King.
He explained that connected solutions, including Thermo King’s TracKing telematics, are bringing refrigerated operations into a new era. “With billions of data points collected weekly, our digital intelligence offerings not only ensure product integrity through the cold chain but can now predict equipment disruptions and offer insights to drive efficiencies for customers’ operations,” he said.
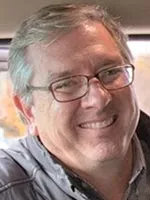
Maddox
Using telematics to monitor refrigerated loads has become the norm rather than the exception. Maddox said fleets are using it to monitor temperatures and TRU performance, automate proof-of-temperature compliance reports, manage asset logistics, minimize dwell time, and address maintenance issues when the trailer is in service.
To help manage reefer requirements, Bison Transport, which ranks No. 49 on the Transport Topics Top 100 list of the largest for-hire carriers in North America, is working with clients to determine what mode is truly necessary for their commodity.
“There is some non-negotiable freight we need to run on continuous. But as trailer technology has increased cooling capabilities of these units, we match this up with product density and work with our clients to determine the proper operating mode for their needs,” Spence said.
He added that minimizing reefer hours reduces maintenance, prolongs the reefers’ life and burns less fuel than running continuously. “The savings are about $32 a day in fuel alone during the peak summer months,” Spence said.
Trailers are often used like extended refrigerators, so they have to run for longer periods, and going green has its challenges. “Significant ones include using alternate power sources outside of a diesel engine to operate the TRU,” Schmeits said. “Others are much simpler and easier to implement at a fleet level. For instance, when to pre-cool a trailer or truck body? How long are the doors open during the load and unload process? Is the equipment well-maintained and operating efficiently?”
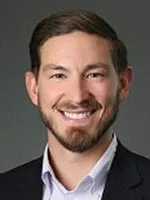
Luzinski
Durm said he frequently sees companies pre-cooling with the trailer door open on the dock, which is ineffective. “A pre-cool has to be done with the door closed. When you’re done, turn the unit off, open the door and load as quickly as possible. Shut the door and turn the unit back on,” he said.
Considering trailer units operating in fleets can spend more than 50% of their operating life in yards, the most effective reduction in diesel use and carbon emissions for a fleet is to increase the use of shore power, Thermo King’s Luzinski said.
The use of electric standby to power TRUs during loading, unloading or staging is trending upward. Carrier Transicold’s Vector trailer units have an all-electric architecture with built-in electric standby capability, and the use of electric standby can reduce operating costs by 40% to 70%, depending on fuel costs, Maddox said.
Maintaining Sustainability
Customers are keying in on zero emissions, trying to deliver products under the correct requirements and conditions without generating carbon. “Driven by regulations, like in California, companies are looking at all-electric TRU systems. Fleets want to be first adopters and we are working on solutions to help our customers get there,” Lee said.
Roeth noted there are several phases trailers are going through as they become more efficient, starting with insulation and shore power and, ultimately, electrification. He expects to see a fully electric system with a battery-electric reefer unit in the future. “Regulations are driving this, but sustainability is becoming a big part of how shippers select carriers. Many companies, whether they are shippers or carriers, have adopted sustainability commitments,” he explained.
Electric units will require shore power to charge batteries before leaving, and the trailer would need enough battery to get through the day and keep the contents cold, Roeth said.
Solar power is one way to help extend that battery life. “Having solar helps to add energy throughout the day to those batteries as you’re depleting them. You can also use regenerative braking. You could electrify the reefer unit without electrifying the truck and vice versa. All of that is being looked at,” Roeth said.
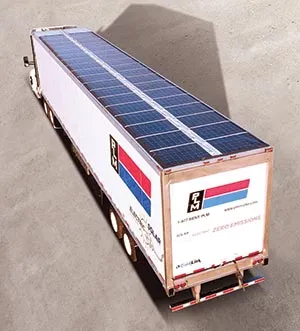
Solar panels help to add energy throughout the day to charge depleted batteries. (PLM)
Merlin Solar has created solar panels that can be applied to the top of trailers and used on all-electric units or with diesel-powered TRUs. “We don’t want to wait for the electrification to happen. We need to be as useful in the diesel world as we are moving to an all-electric world,” said Venkatesan Murali, founder and chief technology officer at Merlin Solar. “Every diesel TRU has at least one battery.”
Merlin Solar’s panels are 3.2 millimeters thick and have a peel-and-stick application, rolling onto the top of a trailer. “The last thing you want to do is make penetrations into a trailer, especially a refrigerated trailer,” Murali said.
Advanced Energy Machines Green has used Merlin Solar’s technology to build 100 units that are in use and has 400 more in the manufacturing chain, said Robert Koelsch, CEO of AEM Green. “We can run just about 100% off of the sun if we maintain a 35-degree load,” he said, adding that AEM’s units have logged 1.8 million hours, 1.8 million deliveries and 8.5 million miles.
PLM offers an all-electric TRU from AEM, which Durm said is ideal for routes that return to base daily. “If we leave on a 97% charge, we return at around 52% at the end of the day. That is a multistop route with a lot of door openings,” he said.
Even still, Koelsch said AEM Green took a trailer from Phoenix to Orlando and maintained a zero-degree box. “Part of that is using a patented wheel-momentum generator. There is a little bit of drag, so it isn’t zero emission, but it is in the 90% reduction range,” he said, adding that the unit can switch to zero emission in areas where regulations require it.
Want more news? Listen to today's daily briefing above or go here for more info
Carrier Transicold’s Vector eCool system all-electric refrigerated trailer system also creates its own power regeneratively while on the road through ConMet’s PreSet Plus eHub system that captures and stores regenerative energy in batteries under the trailer.
Transitioning to electric takes change management, and fleets will have to be intentional about the use of available energy. “Fleets currently plan their routes and operations without much priority given to reefer energy consumption. In an electrified world, fleets will have to optimize route planning to accommodate a more limited energy supply,” Luzinski said.