The Analytical Dilemma
One fleet maintenance executive recently lamented, “The only thing the technicians want to know is where can they find the decision tree to tell them what parts to replace” to know how to respond to a maintenance failure.
In a time when there seems to be a growing reliance on data-driven action items to solve problems, does “old school” detective work still have a part in fleet maintenance programs?
The answer is most emphatically “yes!” — as was made clear during TMC’s fall meeting in Orlando, Fla., through the council’s Technician Electrical Knowledge Assessment, and Trailer Thermal Events Follow-Up Survey, both of which were conducted during the summer. The key lesson learned from each of these research projects was the same: There is a maintenance “analytical gap” in our industry that plays at least a contributing factor to the growing number of unanticipated maintenance failures despite our increasing volumes of telematic data. In today’s “plug-and-play” world, knowing when a component failed is not enough; we also must know what may have precipitated that failure.
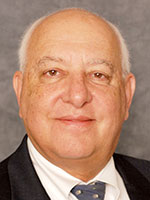
Legler
During July and August, TMC conducted its second survey on wheel-end thermal events to provide more granularity to questions asked of its fleet members earlier in the year. The second survey, conducted jointly by the council’s S.6 Chassis & Brakes and S.7 Trailers, Bodies & Material Handling study groups, concentrated on trailer thermal events in the effort to determine if there were trends in root causation of failures affecting tires, brakes, wheel ends and other components.
It also explored whether drum brakes or disc brakes were more predominantly involved, whether the wheel position on the trailer or combination made a difference and sought to discern if thorough post-incident investigations were being conducted, and if so, what root causes were being identified.
What stood out in the survey results was that there was no close relationship between the number of thermal incidents investigated and those investigations determining the true root cause of the event. Nearly 60% of respondents indicated that they had investigated all of their thermal incidents; only 25% were able to determine a true root cause. The option was given in many questions for the respondents to provide detail as to the methods used in their investigations and the exact causes determined, but comments rarely extended beyond the first or second level of analysis — for example, “tire failure/human error.”
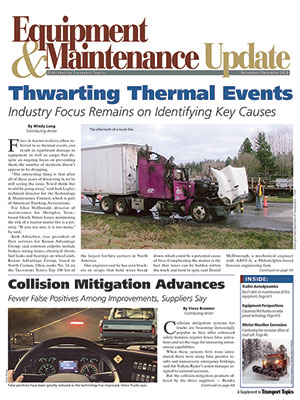
- Collision Mitigation Advances
- Thwarting Thermal Events
- Here Comes the Sun
- The Analytical Dilemma
- Preventive Maintenance Helps Stop Rust Due to Road Salt
- Investigating Thermal Event Causes Is Crucial, Experts Say
- Tire Monitoring and Inflation Systems Can Lead to Fuel Savings, Longer Tire Life
- Seeking Alternative Solutions to Salt
- Don't Skirt Proper Maintenance on Trailer Aero Devices, Experts Say
The survey also asked respondents to rate the effectiveness of corrective actions in reducing the number of thermal incidents. There was an even split between those reporting corrective actions having moderate to substantial reduction as those reporting their actions having minimal to no impact. This split does track closely to the percentage of events in which investigations lead to a root cause determination.
In root cause investigation, three methodologies are commonly used: the “five whys,” the “fishbone diagram” and the “causal tree.” In a highly technical investigation, a combination of these approaches can produce an effective analytic outcome. Failure to fully investigate and follow the trail wherever it leads subsequent to an event or an unanticipated breakdown can lead to erroneous conclusions.
At each stage of investigation that produces data or evidence, a diligent investigator always should ask “why” for each potential causative pathway until that question yields no additional answers. By ruling out multiple potential causes in a systematic manner, the complete modal pathway can be delineated.
The following is a simplified example that illustrates the concept, in which a trailer thermal event has occurred and the investigator pursues this course of action:
• The load was a total loss because a fire originated at the rear inside dual position and penetrated the trailer floor.
• The trailer floor was penetrated because a tire fire produced a sustained flame fed by the tire compounds.
• The tire ignited because the tread delaminated due to overheating recorded in the tire sensors.
• The thermal condition in the tire was a result of wheel end or brake system components overheating repeatedly, causing softening of the tire compound.
• The component overheated (but did not fail) because it was mismatched relative to the other wheel positions in the combination.
• The component was installed correctly during a PMI but was of a specification that did not meet the OEM’s recommendations.
• The incorrect component was provided by the parts department, which ordered it from an aftermarket supplier.
• The part was ordered because management had directed the parts department to reduce costs by going to “off-brand” sources.
In this example, multiple causative points were in the chain, and as TMC observed in its survey, one factor was listed as the root cause, but without further comment or detail. In many cases the root cause may well have been listed as a “tire failure.”
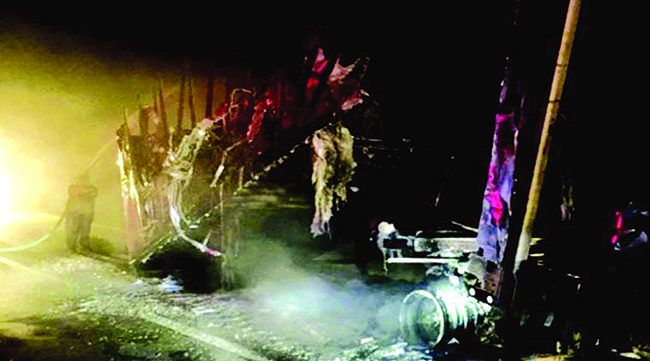
Aftermath of a wheel end-related fire on a trailer. (Technology & Maintenance Council)
While indeed the tire failed and was the proximate cause of the lost load, it did so as a result of another factor. It would have been easy to stop at this point because there likely was telemetry pointing to the overheat in the tire casing, and there were no other “failed” physical components, when the true root cause was a failure of management process.
The critical lesson to be drawn is that if the investigative chain is not followed to its ultimate source, the problem likely will regenerate itself.
Also during TMC’s fall meeting, its S.1 Electrical Study Group presented the results of its Technical Electrical Knowledge Assessment. The assessment evaluated basic electrical concepts, understanding of the multimeter and how it is applied in truck diagnostics, electrical circuit problem solving using readings from the multimeter, and an understanding of the SAE J1939 databus.
The target performance level was 85% in each of the four categories. The actual cumulative results for the 235 participants were:
• Fundamental knowledge 84%
• Application knowledge 75%
• Advanced knowledge 57%
• Databus knowledge 54%
During this presentation, an actual case example was given in which a technician correctly used a multimeter to identify a voltage loss in the electrical system that was causing multiple transmission relay failures. As a result, the alternator was replaced. What was missing in this diagnostic was a failure to identify the actual reason for the voltage drop — in this case, not connecting a ground strap. The result was multiple replacements of relays and alternators because the root cause was not corrected.
In the examples above, reliance on pure data to take action does not result in true correction of the problems encountered.
The challenge is determining what that data means and in applying deductive reasoning to follow the investigative pathways that the data points toward. Maintenance performance, equipment utilization and effective containment of adverse risks to vehicle, drive and cargo hang in the balance.
Jack Legler manages the Technology & Maintenance Council’s recommended practice development process.