Senior Reporter
Shippers, Carriers Race to Prepare for April Start of Federal Food Safety Modernization Regulation
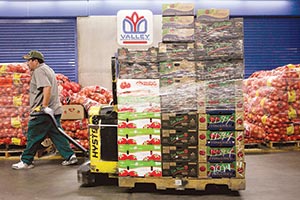
This story appears in the Jan. 9 print edition of Transport Topics.
With the April compliance date for the federal government’s new food transportation safety rule fast approaching, regulators are preparing to clamp down on bad actors in the food supply chain.
But several industry experts agreed that many businesses have been slow to prepare for the U.S. Food and Drug Administration’s regulation on the sanitary transportation of human and animal food, implemented in response to the 2011 Food Safety Modernization Act.
Despite tough talk about enforcement, some in the transportation industry remain “pretty clueless” about the rule, which will force shippers and carriers to have heart-to-heart conversations leading to new contracts or tweaks to existing agreements, said Leonard “Bud” Rodowick, an executive at transport refrigeration unit supplier Thermo King Corp.
In many cases, the comfortable relationships between some shippers and carriers that transport food are about to become a bit more strained, he said.
Everything from the loading dock to the receiver’s dock will need to be documented with procedures, processes, training and records, Rodowick added. “It’s government on steroids.”
Indeed, the scope of the new rule is broad, requiring shippers, carriers, brokers, receivers and loaders to hone their best sanitary food transportation practices.
The 283-page rule places the primary burden on shippers and manufacturers to ensure that the proper written procedures and data collection are in place to keep food properly cooled and trailers cleaned between loads. But it also requires carriers to make good on their promises to shippers.
The new FDA requirements are part of the federal government’s larger effort to prevent food safety problems, rather than reacting to crises when food becomes contaminated.
The final rule’s compliance date is April 6 for large shippers and carriers and a year later for smaller operators.
The original proposed rule raised concerns in the transportation sector, but the final rule is more flexible in allowing the industry to build on its best practices for cleaning, inspection, maintenance, loading and unloading, and operation of vehicles and transportation equipment to prevent food adulteration, the agency’s legal term for food that is contaminated or spoiled.
The regulations exempt food that is fully enclosed by a container, except food requiring temperature control for safety.
“The requirements of the Food and Drug Administration point back to the shipper,” said Jon Samson, executive director of American Trucking Associations’ Agricultural and Food Transporters Conference. “They say whatever the shipper requires, the carrier is going to have to follow.”
In other words, the effects the rule may have on carriers will depend more on shippers’ requirements than those contained in the rule.
“In some of these contracts, we’re seeing quite a bit that’s going to be requested from them, just so the shippers are able to cover their liability,” Samson said. “They’re going to have their own new contracts, and this is how it’s going to be. And if you don’t like it, you’re not going to haul for them.”
Attorneys such as Christopher Ripple who work with motor carriers said that shippers, in some cases, are using the rule to add requirements in carrier contracts that the new regulation may not actually address.
Ripple cautioned carriers to be knowledgeable about the rule so they can avoid taking on greater liability when negotiating new or revised contracts with shippers.
In some cases, food is not covered under the rule for the purposes of food safety, and yet a carrier might still have some obligations to hold that food in certain ways to prevent it from becoming adulterated — even outside of the rule, said Ripple, a regulatory attorney with the Charlottesville, Virginia, law firm of McGuireWoods, whose clients include carriers and food industry firms.
Ripple agreed that carriers and shippers have been slow to embrace the rule, but he has seen movement in recent months.
“Now, suddenly, people are realizing that this is a little bit more than just amending contracts,” Ripple said. “It’s a fuller, broader set of responsibilities that they need to think differently about. Even for clients that have best industry practices, there are still different ways they need to think about framing their obligations to comply with the rule.”
Ripple added, “I think conversations are happening, but I don’t think they’re being resolved quickly. I think that a number of entities are saying that there is much more about this rule that requires closer analysis than perhaps they first thought and that this is not something that people want to wait until the last minute to try to address. Time is of the essence.”
Rob Moseley, head of the transportation industry group for the law firm of Smith Moore Leatherwood, said he believes shippers are way behind in preparing for the food safety rule.
“I feel like people have really dropped the ball when it comes to getting ready for this,” he said.
The rule is all about food safety, not food quality, Moseley said.
“FDA is concerned about food that is rendered unsafe,” he said. “They’re not worried when it went from a two-week shelf life to a five-day shelf life. If it can’t be sold for its highest value, that’s not their problem.”
Although some of the same industry procedures will continue when the rule goes into effect, shippers have said they will become more diligent in checking temperatures, said Scott Cramer, president of Certified Freight Logistics Inc. in Santa Maria, California.
Cramer said his biggest concern isn’t that his customers are telling him how to handle the freight; it’s that his drivers will run into bills of lading with verbiage that he wasn’t aware of.
He said his company plans to try to spot-check those documents to make sure they don’t contain any unex- pected language that shifts liability.
“There are a lot of pieces in this puzzle,” Cramer said.
Tyler Hayes, associate general counsel at refrigerated carrier C.R. England Inc., said one of the more challenging aspects of the rule is that carriers must train all their drivers about the potential food safety problems that may occur during transit.
FDA has promised to post a suggested curriculum for training but has yet to complete the task. At press time, an FDA spokesman had not responded to a request for information on the training curriculum status.
“A lot of the customers are requesting that we keep our refrigeration telematics data longer than we had in the past, but I don’t think we have any obligation to keep those in place any longer because of the rule,” Hayes said. “But producing records within 48 hours after an audit is a little bit different.”
Hayes also said he is convinced that shippers and carriers were late in getting serious about their face-to-face negotiations.
But he cautioned: “I think any carrier is going to definitely need to review carefully all of the food safety requirements that they’re getting from shipper customer contracts, because a lot of them are going to end up coming with more obligations than the rule intended and new ways to create liabilities.”
Hayes added, “Shippers are going to definitely try to protect their interests, but carriers need to be careful to make sure they’re not assuming any obligations that they don’t understand.”
Hayes also said FDA intended for its temperature-deviation requirements to address food safety, not quality.
“I see a tendency in some shipper contracts to just say if you deviate from our temperature instructions, then it will be considered adulterated,” Hayes said. “They’re kind of undoing that buffer zone that FDA wrote into the rule, where it’s not necessarily even a safety-related thing if you’re talking about 2 degrees up or down.”
C.R. England, based in Salt Lake City, ranks No. 23 on the Transport Topics Top 100 list of the largest for-hire carriers in the United States and Canada.
The new food safety requirements also have captured the attention of trucking technology providers, who are seeking to help their customers improve the way they track and record temperature- control information.
“When you move into this, it’s a new world and it’s going to require documented procedures,” said Jerry Robertson, chief technology officer for Bolt System, a provider of fleet management software.