Proper Inflation, Wheel Balancing Help Extend Tire Life, Experts Say
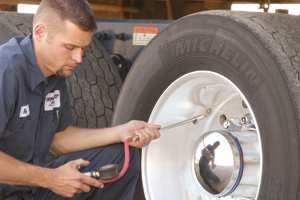
This story appears in the April 27 print edition of Transport Topics.
Preventive tire maintenance handled in-house with everyday equipment is vital for private fleets looking to maximize tread wear and longevity, even for those that outsource some or all of their work, fleet and industry experts said.
“The trend is for all fleets to outsource, but the trend is greater for the private fleet,” said Peggy Fisher, president of the U.S. operations of TireStamp Inc., a tire-management company. “But they still need some tools.” And that starts, she said, with inflation equipment.
Keeping pressure even across tires on a tandem axle is especially important for maintaining even wear, Fisher said. So investment in a multitire inflator — what she called a “four-line spider” — is a good place to start.
The term refers to a shop fabrication in which four pressure lines with valve attachments are hooked to a single compressed-air tapping point. The spider has a pressure gauge that can be set to a specific point. The individual hoses are attached to four tires, which are inflated all at once to the same pressure. This, Fisher said, helps extend tire life by ensuring that all of the tires on a tandem axle will carry identical air pressure rather than having some carry more weight than others.
“If a dual pair has pressures differing by only 3 psi, you will start to see irregular wear,” she said.
There also are purpose-built spider units for the job, including one from Innovative Products of America that can handle all of the tires on one side of a tractor.
“The Mobile Tire Pressure Equalizer is a shop tool that can precisely air five tires at the same time,” said Ian Vinci, the company’s vice president. “The four drive tires are on one circuit, and the steer tire is on the other. Very accurate gauges ensure correct pressures, and the process is far quicker and more accurate than using a single line. Then the opposite side can be replicated.”
Refuse hauler Republic Services in Tampa, Florida, uses it, said Rich Van Remmen, the company’s maintenance manager. Checking air pressure is a regular part of his technicians’ preventive maintenance regimen, and the machine is used to restore the correct tire pressure automatically in his 150 trucks every 2½ to three weeks, he said.
“The real draw is that tires are no longer underinflated,” Van Remmen said. “During the PM, the tech hooks up the equalizer and gets the exact same pressure.” This helps ensure that each tire’s capability is maximized, he said. “All tires do an equal amount of work,” he said.
To inflate tires before installing them on the truck, shop managers should be certain to use a safety restraining device for inflating truck tires, said Rock Tyson, vice president of tire-equipment manufacturer Ken-Tool. The company’s SuperMagnum inflation cage, for example, is designed to accept larger super-wide single tires that are replacing duals on some over-the-road tractors and trailers.
“These cages are able to significantly diffuse the air blast from zipper rupture failures that are common with these new wider tires,” he said.
Inflation cages are but one piece of equipment vital for any shop doing in-house tire service, said Jim Herman, fleet maintenance operations manager for Perdue Foods, in Salisbury, Maryland. Perdue operates more than 600 tractors and 1,400 trailers out of several locations, with a mix of tire-service contracts and in-house maintenance, he said.
“We operate a variety of tire programs, depending on the location,” he said. “Some have mounted-wheel tire service, others mount and dismount. It depends on the size and type of location. All locations, though, have a cage for airing up tires.”
Herman added, “A couple of shops have a bead breaker and equipment to mount and dismount tires. Other locations have only hand tools.”
Shops with a smaller number of trucks may keep tire service in-house so technicians can handle jobs such as refurbishing wheels during slow periods, he said.
They also can keep an eye on tire circumference, which should be measured regularly, Fisher said. And she recommends that after a tire is mounted, whether in the shop or through a mounted-tire program, the circumference be measured and chalked on the tread so matching tires can be mounted as dual pairs. IPA, for example, offers a tool that measures tire size, Van Remmen said.
But all of this attention to air pressure and size can be undone if tires are not balanced. An off-balance tire is not only subject to premature damage and uneven wear, it also can affect fuel economy, said Bob Rutherford, an independent consultant and blogger on tire-related issues.
“The trucking industry is wasting billions of dollars on fuel and tires,” said Rutherford, who has performed fuel-economy research on bead-type balancers produced by equipment manufacturer Counteract. Following testing procedures established by SAE International, Rutherford determined that there was a 2.2% benefit in using the bead-type balancing product versus unbalanced tires.
While Holland Enterprises service manager Richard Houska focuses more on tire longevity than fuel mileage, he is pleased with the results he’s seen from bead balancers from Centramatic used on the fleet’s trucks.
The balancer is a ring that installs on the wheel end. As a wheel turns, beads inside the ring arrange themselves opposite the heavy side of an imbalanced wheel end. This dynamic balancing automatically compensates as the tire tread wears, so repeated balancing is not required.
“We’ve been running them for about four years now, and we don’t balance the tires anymore,” he said. “The Centramatic balances the whole wheel end. It does make the tires last longer, I should think, by about 10%.”
The 450-truck refrigerated fleet is based in Fargo, North Dakota.
Houska said the company is getting 250,000 to 270,000 miles on drive-axle tires, which are moved to trailers when they reach tread depth of 6/32nds to 9/32nds of an inch. They remain on trailers until they reach 2/32nds, which typically means 200,000 more miles of service. “We get 450,000 miles or more from a tire; we don’t run recaps,” he said.
“The reason I use Centramatic balancers is that the wheels are in constant balance all the time,” Houska added. “Balance weights may come off, [but] then the Centramatic balancer would compensate. Now we don’t use weights, as the weights are lead, and lead is expensive.”
For Dunbar Armored, lead weights could be impractical, because most of its 2-axle armored straight trucks — the majority of the company’s fleet of 1,500 vehicles — handle in-town duty. A big issue for these trucks’ tires is contact with curbs, said Doug White, the company’s vice president of maintenance.
“We don’t balance regional city trucks; we hit enough curbs in a month that we’d be throwing the money away,” he said. Instead, White said Dunbar uses Centramatic balancers on the steer axles and is considering installing them on drive axles. “They smooth out the ride, but more importantly, on the smaller trucks, we’re getting better tire mileage,” he said. “When we tried the drive-axle balancers, drivers noticed a difference but didn’t know why, as we didn’t tell them.”
The company relies on Goodyear to handle its tire service. “We’re moving to a fully mounted solution through Goodyear, taking wheels on and off the truck with tires already mounted,” he said.
White said that part of the reason for outsourcing is that the service includes wheel refurbishing. “We can use them to weed cracked wheels out of the system,” he said.
“We do a weekly yard check on tires most of the time,” said Perdue’s Herman. “That more than pays for the effort and time invested in looking after the tires on the fleet.”