Evolving Battery Systems Could Hold Key To Better Reliability, Power Management
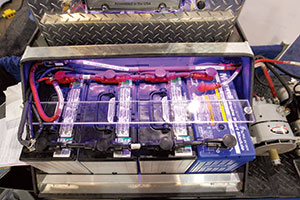
Trucking industry groups and suppliers are exploring a variety of battery technologies that could better manage the power demands of tomorrow’s trucks while providing greater longevity and reliability.
Some industry experts advocate transitioning to higher voltage systems than the current 12-volt standard.
And looking ahead, new technologies that are in the market now or in research labs eventually could overtake the familiar lead-acid battery.
While conventional lead-acid batteries are less expensive than newer technologies, they are relatively heavy and can wear out quickly, especially if they are distressed by heat or other challenging conditions.
At the same time, anti-idling legislation is pushing conventional battery storage to the limit.
Many issues with today’s batteries may be addressed as truck manufacturers and industry organizations examine system voltage.
At the Technology & Maintenance Council of American Trucking Associations, the current feeling is that future trucks would benefit from 24-volt systems.
Al Lesesky, chairman of the future electronics task force under TMC’s Future Truck Committee, said the 12-volt situation in North America compares unfavorably with the 24-volt systems on trucks in much of the rest of the world.
“We’re an island here. With their voltage, truck OEMs don’t have to crimp and solder every terminal. It’s all about power,” said Lesesky, who also is president at Vehicle Enhancement Systems Inc., a research and consulting firm.
While 24-volt systems could be on the horizon, equipment managers for now must work with the products currently in play.
In addition to conventional flooded lead-acid batteries, fleets can utilize valve-regulated lead-acid, or VRLA, batteries — also known to be sealed or maintenance-free.
The two main types of VRLA batteries are absorbed glass-mat, or AGM, and gel.
AGM batteries differ from traditional flooded lead-acid by substituting a fine-glass fiber mat containing sulfuric acid for the liquid electrolyte between the plates.
The AGM configuration offers good deep cycling and may hold a charge up to a year, but carries a mild surcharge over conventional batteries.
Another strategy is to make the electrolyte into a gel. In general, gel batteries have a longer life than AGM batteries and approach twice the life of a flooded battery.
The lead-acid battery, invented in 1859 by French physicist Gaston Planté, predated the first modern car.
But today, battery manufacturers serving various industries are using many other chemistries, including lithium ion, or Li-ion, and, less commonly, zinc-based technologies such as zinc-air, nickel-zinc, or NiZn, and nickel-iron, or NiFe.
Much of the development work has been driven by the desire to gain more range and performance for electric-powered passenger vehicles.
Other alternative battery chemistries include nickel-cadmium, or NiCd, and nickel-metal hydride, or NiMH.
Molten-salt batteries represent yet another technology and already have been used in an all-electric commercial vehicle, the Modec-built eStar van that was marketed in North America by Navistar Inc. between 2010 and 2013.
At the same time, various technologies are under development to increase the charge acceptance, capacity and longevity of the traditional lead-acid battery.
Bruce Purkey, president and chief creative engineer of consulting firm Purkeys Fleet Electric, said paying for a good-quality AGM battery is the answer to criticism of lead-acid technology.
“I disagree that the lead-acid battery is not up to the job,” said Purkey, who also is a frequent TMC contributor on electrical topics. “I’ve been using one particular brand of AGM for my fleet customers — including major fleets who know their costs. I have records that show that 91% of these batteries are still on the truck when traded at five years. . . . Lots of fleets are switching to these AGM batteries, but just like Coca-Cola, you can buy the real thing or you can buy a cheap knockoff.”
Paul Menig was the chief mechatronic engineer for Daimler Trucks and now is a technical consultant. He, too, is a contributor on electrical topics at TMC and a booster for the AGM battery.
“I directed Freightliner to AGM battery technology,” he said. “The biggest reason for the switch was the balancing act we must do between starting and hotel loads. AGM was a way of accomplishing that — a better alternative at the time.”
The problem with lead-acid longevity is due more to the environment on the truck than a failing of the chemistry, he says.
“The problem is we’re taking too much out of the battery, especially since trucks must operate down to minus 40 degrees and up to increasingly high temperatures. The last three summers have been particularly hard on batteries.”
Changing truck design also has an effect.
“Some OEMs got caught in the hot weather where they ran exhausts too close to the batteries,” Menig said. “And more aerodynamic side fairings are preventing the cooling air reaching the batteries. When a truck is stopped, engine heat today is being transferred into the batteries as well.”
Menig said efforts to use waste-heat recovery as a fuel-saving technology also could exacerbate issues with overheated batteries.
“I hope we will see a move to 24 volts as engine compartments get more crowded and heat is an issue. A 24-volt alternator and starter are smaller and free up some space,” he said.
Some fleets are having success with hybrid battery systems that combine a super- or ultra-capacitor storage battery for starting load and AGM batteries for the truck “hotel” loads. Both Kenworth and Peterbilt offer Maxwell’s engine-start module.
Bill Turner manages a fleet of 65 trucks that includes many transit mixers for Holroyd Co., based in Washington state. He initially tried Maxwell’s ESM on six Kenworths.
“I discovered that the ESM starts the truck without failure. You have to have these trucks ready to roll,” Turner said. “The first thing that goes through my mind is, if it’s a mixer truck — is it loaded? If it does have a load of mix in the drum, that changes everything. I want to know what’s our fastest way to get this thing to run.”
In the broader scope of battery technologies, there’s a lot of talk about lithium-chemistry batteries, not least because luxury-car maker Tesla is using Li-ion for its cars. Tesla’s outspoken principal, Elon Musk, is center stage in the electric-vehicle business and not just because of his remarks. He is putting his money where his mouth is, investing in a $5 billion production plant to churn out Li-ion cells that, in their thousands, make up the battery packs that lurk under the floor of the Tesla S luxury cars.
Tesla’s plant, when it goes on stream in three years, will be able to produce 500,000 battery cells per year — production in excess of all the Li-ion capacity currently in the world. This “gigafactory” production exceeds, by a factor of three to five, the production needs for current and anticipated volumes of the Tesla car.
And in a field where research is ongoing, there’s the accusation that building this plant is a bet against something better coming along. Musk counters any suggestion that his battery technology may be outdated by any new discoveries. He stated in June 2014 that he had not seen any new “battery breakthroughs” that are better than the Li-ion batteries currently deployed in the Tesla electric vehicles.
Li-ion also is perceived as a winning technology by battery expert Isidor Buchmann of Vancouver, British Columbia-based Cadex Electronics Inc., a company focusing on battery diagnostics and monitoring to extend battery life and reliably predict battery failure.
“The two winning chemistries are lead-acid and Li-ion,” Buchmann said.
He sided with Musk on alternative battery technologies.
“Besides new and experimental batteries, the solid-state battery is also getting much attention but they could be years away from commercialization,” Buchmann said.
The sheer volume that Tesla intends to produce could help drive Li-ion into applications currently dominated by lead-acid. The production of so many cells should drive down costs of Li-ion batteries, which takes away the major disincentive to using them for vehicle starting, lighting and ignition.
With the barrier of cost lowered, the benefits are significant. Size for size, lithium-based technologies promise improved performance with faster charge acceptance, better cycle life and up to a 60% weight reduction compared with a lead-acid battery.
However, lithium-ion cells are capable of going into “thermal runaway” in which the cell rapidly heats and can emit flames and dangerous fumes. The likelihood of that is potentially high for lithium-ion as it has a high amount of energy in a small volume. Multiple cell and pack safety precautions have to be taken to prevent fires, but they add to the cost. Tesla has not had such an event, but the early Boeing Dreamliner battery fires have demonstrated the fire potential of Li-ion batteries.
Meanwhile, nickel-zinc battery chemistry is having some success in the new generation of microhybrids. These are the passenger vehicles that feature stop-start technology, shutting down whenever the vehicle wheels stop turning and firing up again the moment the accelerator pedal is pressed. Since the starter motor is in use many more times during driving, a newer technology than even the most advanced lead-acid has proved itself necessary, and NiZn is the chosen technology for a number of car manufacturers.