Senior Reporter
ATRI Tallies Environmental Impact of Zero-Emission Trucks
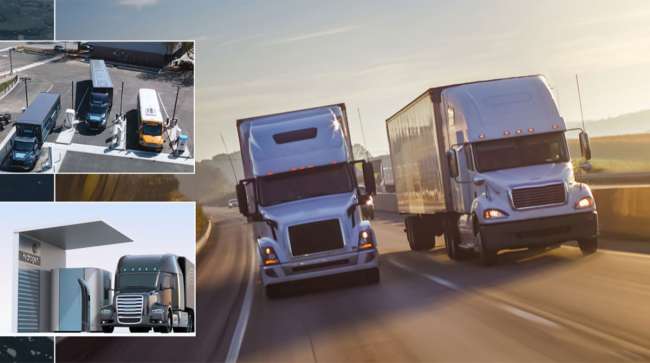
[Stay on top of transportation news: Get TTNews in your inbox.]
The overall life cycle of Class 8 zero-emission trucks would result in a net decrease in carbon dioxide emissions of just 30% compared with internal combustion engines despite the trucks having no direct tailpipe emissions, according to a just-released study by the American Transportation Research Institute.
The report, titled “Understanding the CO2 Impacts of Zero-Emission Trucks,” determined that CO2 emissions generated during the production of electricity and hydrogen — both of which are used to power zero-emission trucks — along with production and disposal of the electric storage equipment, lithium-ion batteries and the vehicles themselves all contribute to their overall emissions impact. The report’s key finding is that zero-emission trucks still generate significant overall life cycle CO2 emissions, and will continue to produce CO2 emissions in the coming decades.
“The core motivations for a shift to ZETs remain environmental, and it may be possible to decrease the trucking industry’s emissions through their deployment — although the scale of environmental benefit is unclear,” the report stated. “This research provides industry, government and other stakeholders with a technical environmental impact assessment of switching to ZETs, as well as a glimpse at the advancements that may be needed to further decrease industry emissions.”
.FOR IMMEDIATE RELEASE: New #ATRI Research Quantifies the #Environmental Impacts of Zero-Emission Trucks https://t.co/f2Y5cufo1j #TruckingResearch #carbonreduction #electrictrucks #zeroemissions — ATRI (@Truck_Research) May 3, 2022
The report lands as “a movement toward zero-emission vehicles has strengthened in recent years, particularly through state-level environmental goals and regulations,” ATRI noted.
The report, released May 3, studied the life cycle CO2 emissions of three Class 8 sleeper cab trucks; one battery-electric, one hydrogen fuel cell electric and one a traditional diesel. ATRI drew on outputs from the Argonne National Lab’s GREET Model’s life cycle data.
According to the detailed 43-page study, the environmental benefits of electric trucks are offset due, in large part, to lithium-ion battery production.
For the three vehicles, the total emissions of CO2 emitted during production, converted into pounds of CO2, were 478,055 for a battery-electric truck compared with 115,514 pounds for a fuel cell electric and 74,728 pounds for an internal combustion engine-powered truck. The CO2 emissions calculated for BEV battery production included two 1,622 kWh batteries — one with the original truck, and the second for a replacement installed at 500,000 miles.
The report also incorporates CO2 emissions the U.S. electrical grid generates through its reliance primarily on fossil fuels.
ATRI noted, however, that several potential benefits to electric trucks that are not the focus of this paper include diversification of energy sources, along with smoother ride qualities for trucks, better acceleration and less complicated repair and maintenance, among others.
Most of government and industry’s recent focus on zero-emission vehicles has been on what leaves the tailpipe. ATRI’s report draws attention to the useful life of a BEV and the pros and cons of battery recycling, or “farming” old but not depleted batteries. It also focused on where, when and how electricity from the grid is produced, how hydrogen is produced and delivered, and sourcing and supply chain issues.
Federal and state mandates to make heavy-duty diesel engines even cleaner are approaching. The most realistic approach to decreasing ICE C02 at the tailpipe is through alternative fuels such as biodiesel, renewable diesel and natural gas, ATRI said, citing the Diesel Technology Forum.
U.S. vehicle manufacturers are researching next-generation batteries that have attributes such as faster charging, lower cost and higher energy capacity. One concept involves solid-state batteries, which in theory could meet these requirements, ATRI said. Barriers to using this technology do exist, however.
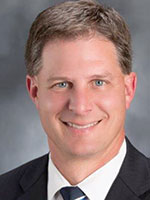
Ekberg
ATRI concluded hydrogen fuel cell trucks are “ultimately the most environmentally friendly truck type, although the technology is not presently feasible for longhaul operations.”
“The U.S. trucking industry is strongly committed to carbon-reduction efforts, and electric motors and drivetrains offer many additional performance and maintenance benefits,” Hugh Ekberg, CEO of CRST, said in the release announcing the study. “But ATRI’s research highlights that several of the leading zero-emission approaches being advocated today still need additional research to fully understand how the different technologies can be best developed and utilized to maximize carbon reduction.”
CRST The Transportation Solution ranks No. 24 on the Transport Topics Top 100 list of the largest for-hire carriers in North America.
A new Class 8 diesel truck tractor may cost roughly $135,000 to $150,000, and the purchase price of a new Class 8 BEV can be as much as $450,000 (before possible incentives), according to ATRI.
Want more news? Listen to today's daily briefing above or go here for more info
ACT Research estimates that the battery pack for a Class 8 BEV accounts for roughly 55% of the cost of the BEV truck. This cost, in theory, may fall as battery production and the extraction of raw materials expand, the report pointed out.
ATRI said estimates for a Class 8 fuel cell truck range from $200,000 to $600,000 (before possible incentives) with 60% solely credited to the fuel cell propulsion system. The hydrogen storage system is estimated to account for 20% of the total vehicle cost.
The report is available at truckingresearch.org.